Part 3: Electronics Materials Management in EMS Manufacturing Factories
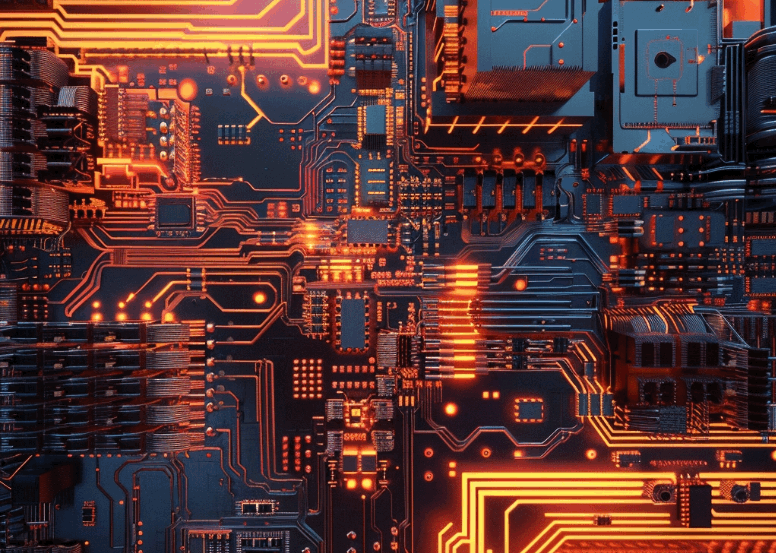
As I outlined already in part 1 and 2, below are some additional metrics used by savvy EMS manufacturers keeping close eye on components inventory and materials used in OEM customer programs. EMS manufacturing industry produces a lot of revenue from warehouse and inventory management so its important to identify and manage granulated costs as much as possible - for EMS and OEM firms, alike.
OEM program managers with EMS program oversight can benefit their OEM enterprises tremendously in terms of total EMS program cost/spend, and EMS provider accountability, by paying close attention to 'how' EMS manufacturers are charging for warehousing services.